Comprehending the Basics of Plastic Injection Molding Processes
Plastic injection molding offers as a keystone of modern manufacturing, giving a systematic technique to producing complex components with accuracy. Discovering these essential aspects can disclose how even small changes can lead to significant enhancements in production outcomes, raising concerns concerning the possibility for advancement in this recognized procedure.
What Is Plastic Injection Molding?
Plastic injection molding is a commonly made use of production process that changes thermosetting and thermoplastic products into specific and complex shapes. This technique is favored for its capability to produce high volumes of identical components with phenomenal accuracy, making it an indispensable approach in different sectors, consisting of auto, durable goods, and clinical devices.
The procedure entails melting the picked plastic material and infusing it right into a mold and mildew under high pressure. The mold and mildew, made to the requirements of the preferred part, allows the molten plastic to take shape as it strengthens and cools down. Once the material has actually solidified, the mold is opened, and the finished element is expelled.
Plastic shot molding offers numerous advantages, including reduced waste, uniformity in manufacturing, and the capability to include detailed layouts that may be challenging with other making methods. Furthermore, it supports a wide series of products, each providing unique residential or commercial properties that can be customized for specific applications. As industries continue to introduce, plastic injection molding continues to be at the center, allowing the advancement of sophisticated products that fulfill advancing customer needs.
The Injection Molding Refine
The injection molding process is an advanced strategy that entails several key stages to generate top notch plastic elements. At first, plastic pellets are fed right into a warmed barrel where they are thawed into a thick fluid. This molten plastic is then infused under high pressure right into a precision-engineered mold, which forms the product into the desired type.
As soon as the mold and mildew is loaded, the plastic is allowed to solidify and cool down, taking the form of the mold cavity. Air conditioning time is crucial, as it influences the cycle time and the final properties of the shaped component. After adequate cooling, the mold opens up, and the ended up component is ejected using ejector pins.
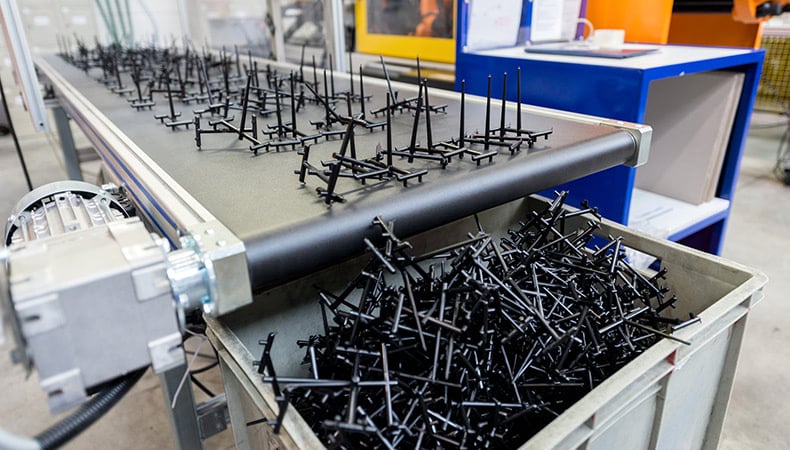
Materials Made Use Of in Injection Molding
Different products can be utilized in the injection molding procedure, each offering one-of-a-kind residential or commercial properties that deal with details applications. The most frequently used materials include thermoplastics, thermosetting plastics, and elastomers.
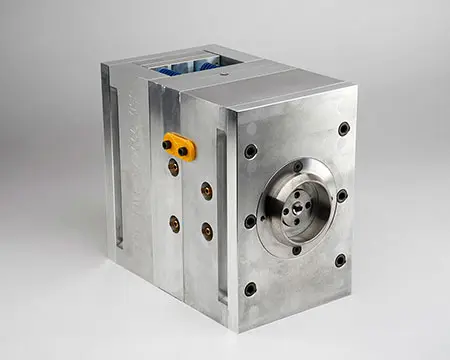
Thermosetting plastics, like epoxy and phenolic materials, go through a chemical modification throughout the curing process, leading to a stiff, inflexible structure. These materials are optimal for applications needing high warm resistance and structural honesty, typically made use of in electric insulators and vehicle components.
Elastomers, consisting of silicone and rubber-based find out materials, give flexibility and durability. Their special buildings make them appropriate for applications that demand elasticity, such as gaskets and seals.
Furthermore, specialty products like bio-based plastics and composites are gaining grip for their environmental advantages and improved performance qualities, broadening the extent of injection molding applications in numerous industries. Understanding the properties of these materials is crucial for selecting the ideal type for specific jobs.
Advantages of Injection Molding
Injection molding sticks out as a highly reliable manufacturing process that provides countless benefits for generating intricate components with accuracy. One of the most considerable benefits is the capability to produce intricate designs that would be impossible or difficult to accomplish with other approaches (Plastic Injection Molding). The process permits limited tolerances and in-depth attributes, making certain high-quality parts
Additionally, shot molding is known for its fast manufacturing capacities, making it an ideal choice for high-volume manufacturing. When the mold is developed, parts can be created swiftly, reducing lead times and boosting news overall efficiency. This performance not only decreases production expenses yet likewise gives an one-upmanship out there.
The versatility of materials made use of in shot molding additionally improves its charm. A wide variety of thermoplastics and thermosetting polymers can be employed, allowing suppliers to select materials that best satisfy their particular requirements, consisting of flexibility, warmth, and stamina resistance.
Furthermore, the process minimizes waste, as excess product can often be reused and reused. This sustainability element adds to a reduced environmental influence, making injection molding an accountable manufacturing choice. On the whole, the advantages of injection molding make it a preferred method for several industries.
Variables Impacting Item Quality
While numerous factors can influence product top quality in shot molding, comprehending these elements is crucial for achieving optimum results. Key aspects include product selection, processing parameters, and mold and mildew style.
Material selection plays an important duty, as different polymers show unique residential or commercial properties that influence flowability, strength, and thermal stability. Inadequate material selection can cause defects such as bending or insufficient dental filling.
Handling criteria, including cycle, pressure, and temperature level time, have to be carefully managed. Variations in these settings can lead to incongruities in component dimensions and surface area finish. For instance, excessively heats may cause deterioration of the polymer, while insufficient stress can result in brief shots.
Mold and mildew design is just as essential, as it establishes the circulation of the molten plastic and the cooling procedure. Improperly developed mold and mildews might bring about uneven cooling prices, causing residual stress and anxieties and dimensional mistakes.

Verdict
Finally, plastic shot molding acts as a crucial manufacturing process that allows the efficient production of top notch components. Proficiency of the shot molding process, including the understanding of products and the impact of various elements on product quality, is crucial for attaining optimal results. The advantages of this method, such as cost-effectiveness and design adaptability, additional emphasize its significance throughout numerous sectors, strengthening its condition as a preferred selection for high-volume production.
Plastic shot molding offers as a cornerstone of contemporary manufacturing, supplying a systematic strategy to generating intricate elements with precision.Plastic shot molding provides several benefits, including reduced waste, uniformity in manufacturing, and the capacity to incorporate elaborate styles that may be challenging with other making techniques (Plastic Injection Molding). As markets continue to introduce, plastic injection molding stays at the center, making it possible for the development of innovative products that fulfill progressing customer demands
The injection molding procedure is a sophisticated method that entails several vital phases to generate top notch plastic official site elements.In verdict, plastic injection molding offers as an essential manufacturing procedure that allows the effective production of high-grade components.
Comments on “Checking out the Future of Plastic Injection Molding in the Production Industry”